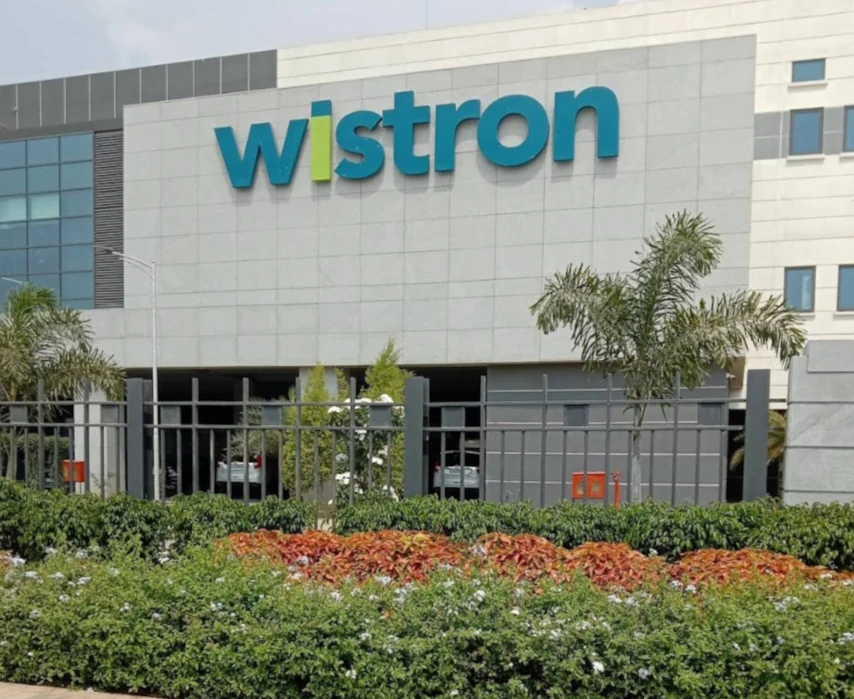
India is finding early success in its endeavor to position itself an alternative manufacturing destination to China in electronics, said US-based Morgan Stanley in its report – Multipolar World: Tech Supply Chains Make India the Next Stop.
The shift is being driven by a combination of rising costs in China, supply chain risks, geopolitical factors and specific policy initiatives taken by the Indian government.
The report points to a “major reconfiguration of global tech supply chains” and how India could be the next big beneficiary as companies look to diversify their manufacturing bases beyond China. It points out that Vietnam — which it calls the new Guangzhou — has had tremendous success as one of the early destination.
The report notes that this trend is being shaped by two key needs – hedging risks by shifting production capacity around China, and ‘friend-shoring’ which involves companies moving manufacturing to geographically and politically aligned nations.
India, with its large domestic market, young demographics, skilled labour pool and government incentives, seems well placed to gain from these shifts, Morgan Stanley said.
The financial services firm expects India’s electronics manufacturing industry to expand at a 21% every year over the next ten years to reach $604 billion by FY32 from $87 billion currently.
Out of the $604 bln, mobile phone manufacturing, which has already seen big growth under the government’s production-linked incentive (PLI) scheme, will expand to $235 billion by FY32.
Overall, the bank expects India’s share in global electronics production to rise from 3% currently to 4-5% by 2025.
However, the report caution that India still faces stiff competition from manufacturing hubs in South East Asia. And building complex semiconductor supply chains will require policymakers to address issues like infrastructure gaps, skill shortages and easing the costs of doing business.
India’s traditional backwardness in electronics manufacturing
For decades, India has punched below its weight in electronics hardware manufacturing. The country directly evolved from an agrarian economy into a services-led economy, without creating a strong electronics manufacturing base like China.
As Morgan Stanley analysts note, India’s share in global electronics production was just 1% in 2012. The country has heavily relied on imports to meet even domestic demand, given an underdeveloped local manufacturing ecosystem.
There are several structural factors that have inhibited the growth of electronics manufacturing in India:
Lack of component manufacturing base: India has traditionally lacked a components manufacturing base, which is critical for a vibrant electronics industry. It has had to depend on imports for key components like semiconductors, displays, printed circuit boards, connectors etc. Setting up component manufacturing units requires large investments and advanced technical know-how that has been lacking.
Higher costs of production: Factors like complex regulations, inadequate infrastructure, limited financing, high power tariffs and inefficient logistics have made India an uncompetitive manufacturing destination resulting in higher costs than peers like Vietnam and China. This made imports cheaper than domestic production.
Low R&D investments: Electronics manufacturing requires significant R&D investments to keep pace with rapid technological advancements. However, investments in R&D by both government and private sector have been low historically. This inhibited innovation and creation of a robust manufacturing ecosystem.
Labour regulations and skill gaps: Traditionally, India’s labour laws have been rigid with restrictions on hiring and firing. Skilled workforce trained specifically for electronics industry has also been in short supply. This added to costs for manufacturers.
Underdeveloped supply chains: India’s electronics supply chain has been fragmented with lack of linkages between different nodes of manufacturing. This deterred large-scale manufacturing investments.
High import tariffs: For instance, high levies on imported components like PCBs made the final electronic products less competitive compared to imports, the report pointed out.
Minimal trade agreements: India’s engagement with free trade agreements has been limited, which inhibited integration with global electronics supply chains and ability to leverage duty concessions.
Lack of export incentives: India did not have significant incentives for exports of electronics unlike Vietnam which used duty rebates to boost manufacturing exports.
Thus, due to these multiple disabilities, India could not develop a competitive domestic electronics manufacturing industry. Its value add in the global electronics supply chain remained miniscule at around 1-2%.
In contrast, China adopted a very different policy approach since the 1980s that allowed it to become the undisputed leader in electronics manufacturing. Through special economic zones, tax breaks, export incentives, subsidized infrastructure and land, China created a vibrant ecosystem that led to dominance in sectors like mobile phones, computers, LEDs and solar equipment.
Today, China accounts for nearly 50% of the $2.5 trillion global electronics manufacturing services market. Its success convinced many countries that electronics manufacturing could be a pathway to prosperity and rapid economic growth. India has been a laggard on this front.
But over the past decade, especially since 2014, India has begun making amends. The government has recognized electronics manufacturing as a key priority area and taken steps to boost India’s competitiveness as a manufacturing destination.
Rethinking China as the sole manufacturing base
Since the early 1990s, China has been the dominant destination for technology manufacturing investments by global brands. Its scale, supply chain clusters, strong infrastructure and low costs allowed China to become the factory to the world.
However, in recent years, there has been a rethink about excessive dependence on China as the sole manufacturing base due to a confluence of factors.
First is the rising labour and regulatory costs that have made manufacturing in China less competitive compared to a decade ago, with wage growth in double digits, pointed out Morgan Stanley.
Secondly, the COVID pandemic has been an eye-opener as China reeled under recurring lockdowns.
Geopolitical tensions, especially between US and China, have added uncertainties for companies over relying completely on Chinese factories.
Moreover, there are worries around intellectual property security and technology de-coupling.
As China has climbed technology value chain, it is incentivizing localization of higher value-added production like electronics components. This has also nudged foreign companies to diversify manufacturing.
Finally, developed economies like US, Japan and South Korea are providing incentives to technology firms to re-shore production capacity closer home to boost jobs and manufacturing competitiveness.
As a result, technology brands have been actively looking at alternative manufacturing locations to reduce over-dependence on China.
Countries like Vietnam, Thailand, Indonesia and Mexico have benefitted from these diversification efforts.
For instance, companies like Samsung, LG, Google and Apple have set up new factories in Vietnam in the last 5-7 years. The Vietnam government has offered companies special economic zones, tax holidays and duty rebates to incentivize investments. Vietnam has become a key rival to China in electronics exports.
India believes it can also benefit from these supply chain shifts away from China, especially in mobile and electronics component manufacturing.
According to Morgan Stanley, China’s share in US imports peaked at 22% in 2017 but has since dropped to 17% in 2022 as re-shoring and friend-shoring accelerates. The bank expects technology supply chains to become increasingly regionally concentrated in Asia.
As companies adopt a “China + 1” strategy, India emerges as a strong contender given its market size, demographic dividend, low costs and policy incentives.
Indian government’s incentives
India has always been trying to attract foreign investment, from the time of the second UPA government in the early 2010s.
Among the notable initiatives is Make in India lunched in 2014 with the aim of boosting domestic manufacturing across 25 sectors, including electronics.
The uniform Goods and Services Tax or GST regime has helped create a common market and reduced tax complexities compared to the earlier system.
Another big differentiator has been PLI schemes or Production Linked Incentive schemes, which offer 4-6% incentives on incremental sales of manufactured goods in India to encourage local production and exports.
Additionally, state governments like Tamil Nadu, Telangana, Karnataka and Gujarat have their own policies and incentives to attract electronics manufacturing investments.
This combination of progressive central government policies and competitive state-level incentives have helped turn India’s narrative as a manufacturing destination.
Morgan Stanley points out that the government’s target is to create a $300 billion electronics manufacturing industry in India by 2026. It expects exports to rise from $10 billion now to $120 billion by 2026.
The Vietnam Story
One of the inspiring stories for India has been the emergence of Vietnam as one of the biggest beneficiaries of these supply chain shifts, especially in electronics.
The Southeast Asian nation has successfully managed to position itself as an alternative electronics manufacturing hub thanks to strong government support and strategic trade policies.
According to Morgan Stanley, Vietnam’s electronics exports have registered meteoric growth from around $2.2 billion in 2007 to nearly $61 billion by 2017. Exports expanded at a scorching 56% CAGR between 2011-17 as more production shifted from China.
Vietnam has become the second largest exporter of mobile phones behind only China. Key phone makers like Samsung, LG and Foxconn have massive factories in Vietnam now. Apple is also planning to manufacture MacBooks and iPads in Vietnam via Foxconn.
Much like China in the 1980s and 1990s, Vietnam too focused on first attracting large-scale investments in electronics assembly to gain global scale. Policymakers then worked on localization of components manufacturing to move up the value chain.
The Vietnamese government gave a big push to electronics manufacturing through a slew of policy measures, such as tax holidays — including corporate income tax waivers for 4 years followed by 50% tax reduction for another 5 years. In fact, high-tech manufacturing projects got 30-year tax holidays.
It also gave import duty exemptions, Subsidized infrastructure such as land, industrial parks with utilities, accommodation and transport, and finally, it entered into trade agreements with Japan, EU, US and ASEAN.
Proximity to existing electronics supply chains in China and Taiwan was also a key factor that allowed companies to easily integrate Vietnam into production networks. Samsung now has half its global phone capacity in Vietnam.
According to Morgan Stanley, Vietnam’s success factors like competent infrastructure, attractive incentives and young workforce make it the benchmark that India has to match or better to become the next Asian electronics tiger.
The Indian government has made a promising start through schemes like PLI, Phased Manufacturing Plans and Electronics Clusters. But there is still significant scope to enhance India’s competitiveness relative to manufacturing powerhouses like Vietnam and China.
Challenges for India
While India has potential to be the next leader in electronics manufacturing, aided by government incentives, it still faces considerable challenges that need policy attention:
Infrastructure gaps: Issues like power cuts, inadequate water supply, congested ports and roads add to costs for manufacturing units in India compared to the clusters in Vietnam and China where reliable utilities and connectivity are available.
Lack of skilled workforce: As per industry estimates, only about half of India’s engineering talent is readily employable currently. Vocational training in electronics needs scaling up rapidly to build workforce capacity.
Higher costs: Factors like industrial power tariffs, logistics and cost of financing still make India less competitive than Vietnam or Indonesia in electronics assembly. Subsidies help but disabilities exist.
Domestic supply ecosystem: India still depends heavily on imported components like semiconductors, displays, printed circuit boards etc. Nurturing component manufacturing locally essential to move up value chain.
Complex regulations: Obtaining land, environment approvals and complying with inspections by multiple agencies increases compliance burden. Single window clearances can help.
Higher import tariffs: Import duties on components like printed circuit boards remain high in India, inflating the cost of manufacturing electronic end-products domestically. Rationalisation of tariffs critical.
Focus on execution: While schemes like PLI have boosted interest, the government must ensure seamless disbursement of incentives. Delays or complex paperwork could undermine the progress.
State-level support: Success stories like Vietnam show that states also have to compete to attract manufacturers by improving infrastructure and providing incentives over and above central schemes.
Innovation ecosystem: R&D investments are vital to indigenous product development and owning IPRs. But India invests less than 1% of GDP in R&D. Focus needs to be on creating a vibrant innovation ecosystem.
Foreign investors also face some challenges unique to India like anomalous high taxation imposed retrospectively, delays in contract enforcement through lengthy litigations, recent withdrawal of export incentives through schemes like MEIS etc.
Strengthening infrastructure, undertaking reforms to reduce business costs, investing in skills, building domestic supply chains and maintaining policy stability are key to maximising India’s potential as a champion electronics manufacturer according to Morgan Stanley.
States like Tamil Nadu and Gujarat will play an influential role in this process, the brokerage said.
Early signs of success
While considerable scope for improvement exists as discussed above, India has also seen some early successes that indicate its technology manufacturing industry could be at an inflection point.
First is the smartphone success story. From just two factories in 2014, India today has 268 phone factories producing nearly 300 million smartphones per year. Leading brands like Samsung, Apple, Xiaomi, Oppo and Vivo have set up large plants. Total electronics exports are up from $6 billion in FY15 to $15 billion now.
Secondly, global electronics contract manufacturers like Foxconn, Flex and Wistron are rapidly expanding existing facilities or setting up new factories across India to capitalise on incentives.
Similarly, in component manufacturing, Firms like Ascent Circuits, Syrma, Valenkani have begun manufacturing PCBs, molds and dies locally as first steps. Foxconn plans to commence PCB production in India as well.
This has led to the emergence of electronics manufacturing clusters in places like Andhra Pradesh, Tamil Nadu, Telangana, Uttar Pradesh and Karnataka.
Encouraged by a supportive government, groups such as Vedanta and ISMC have shown interest in putting up chip fabs
While Vietnam is currently ahead, India could catch up rapidly with its larger scale and domestic demand potential if the government maintains its supportive stance and policy momentum and addresses key bottlenecks.
According to Morgan Stanley analysts, if India manages to capture even 4-5% share of the global electronics manufacturing services market by 2025 from 1-2% currently, it translates into a $190-200 billion opportunity.